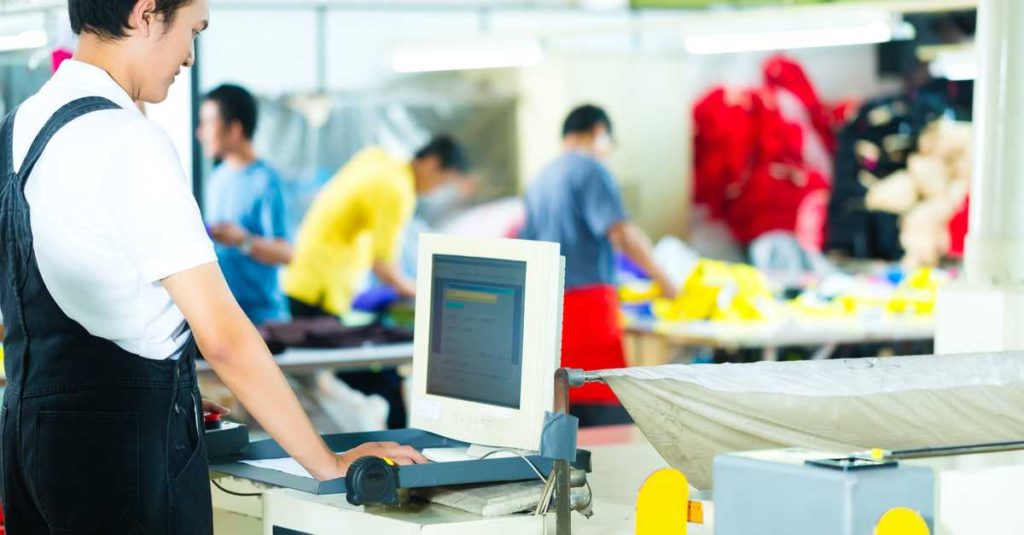
Documenting the standard way of performing production and inspection work is part of the ‘best practices’ all good manufacturers follow. However, we have seen many bad examples of bad work instructions (WIs), as well as a few very good examples.
Here is a list of tips to prepare good WIs.
1. Think of how the work has to be done, as a process
A process has input(s), has an activity that can be broken down in discrete steps, and has output(s). One key objective here is to show how each step is to be done. So, start by asking, what are those steps, and can we think of one ‘best way’ of performing those steps?
if the workers can give their input, that’s great! They will be much more likely to follow the WI.
2. Make it visual, with a minimum of text
Most people grasp a graphical explanation faster and better than a written set of instructions. A company that does this very well is IKEA.
Here is an example.
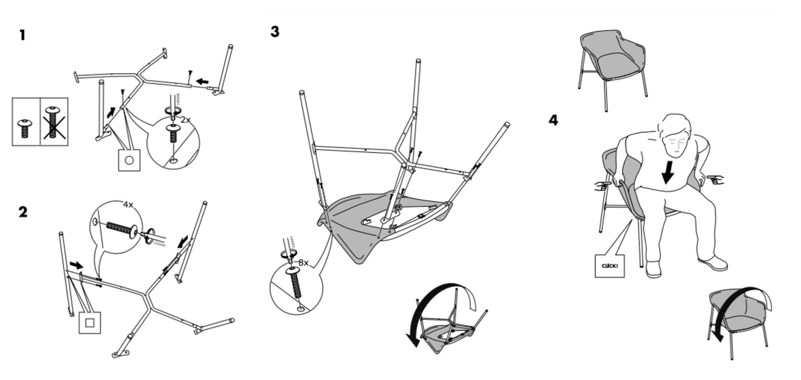
(Image source)
Even better, show color images or illustrations. Black and white is not the best at grabbing people’s attention.
3. Include the key attention points
Include photos or drawings of potential issues (and you should probably have an idea of these issues – ideally you have performed a process FMEA and a pilot run before going into mass production).
Again, let’s look at an example from IKEA:
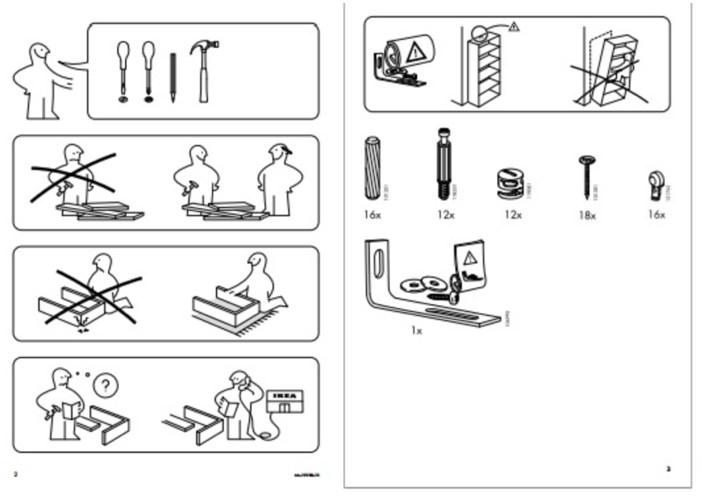
(Image source)
4. Mix some transformation and some testing/inspection
When designing the process, don’t think each workstation has to do only transformation work or only testing work. If a part or a sub-assembly is defective, letting it go down through the processes adds more and more waste!
Production operators can usually do self-inspection, or (better) successive inspection on the parts they get from the upstream processes.
For the same reason, if a testing station has a low cycle time, do you want that testing operator to be idle and wait for upstream parts? She might be able to do an operation before or after the testing, so that the line gets more balanced.
5. When equipment is used, does it make sense to include maintenance-related work?
At the very least, workers should clean the equipment when taking their shift and just before stopping. Sometimes that work is spread along the day, and it can be merged with 5S activities. All this can be documented in a work instruction, too.
6. For quality inspection/testing work, document the sequence but also the standard
When it comes to inspectors and testers, there is often a process to follow (involving a standard sequence of steps). There are also failure modes, and these often necessitate a number of photos as well as samples. It usually cannot all be in a WI… but the WI can illustrate the most common defects.
7. Put the work instructions in the right place for those who need to read them
Once the operators have been trained, they are left to work independently under the supervision of the local line leader. Who should look at the WI, then?
- The operator, when he has a question? That’s possible, especially if the work is complex (e.g. long cycle time) and is often switched from one product to the next.
- The line leader, when he walks around and ensure all is done to standard?
Really, there is no good answer here. It depends on the context and the needs.
8. Keep it updated
One challenge in many factories is that things change. A line is used to assemble product A, then product D, then product X. A process engineer comes up with a better way of doing something. A customer asks for an engineering change. And so forth.
If you manage Work Instructions on paper, it will be a lot of hassle to keep it all updated. It adds work to the line changeover routine.
Displays are sufficiently inexpensive nowadays that you may want to “go paperless”. A simple MES system can ensure the latest version of each WI is shown on the right work station at the right time. This is still relatively rare in China, but it will become increasingly common.
9. Work on improving the process; it is never fully optimized!
Earlier, we wrote “think of one ‘best way’ of performing those steps”. That’s the ‘one best way’ known and recognized at that time. There is virtually always a better way!
If a production is done in high quantity, a little improvement every week will translate to pretty serious savings.
If updating and approving new WIs is very cumbersome, your process engineers might hold back. Make it easy for them!
We’re here to help you!
Do you have any questions about this topic or experiences to share? Maybe you need help with developing and manufacturing your product? Please leave us a comment or hit the button to contact us: