How We Help You Ensure the Safety of Your Products
Understanding the safety regulations of the countries in which you sell
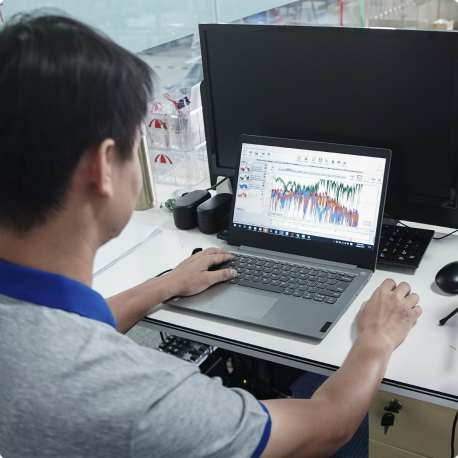

Confirming reliable product designs
Most safety issues come from a faulty design. While we can’t pretend we will detect those issues when reviewing your design files, we do have a mature process for testing the reliability of prototypes and providing feedback. We do some tests in-house and others in a local laboratory.
A reliable product is much less likely to lead to catastrophic failure in the hands of users. For example, an e-bike has a brake system that MUST NOT fail even in the rain, in very low temperatures, after 3 years of intense usage, etc.
Appropriate procurement strategies
Purchasing high-risk parts such as chargers or batteries from small and untested manufacturers that can show no relevant certificates is highly risky, and it will call for a much more expensive testing plan. That’s an example of a mistake to avoid.
Our customers always get the Bill of Materials, and they can see the ways we qualify the component suppliers (through audit reports, among others), so there is a lower risk of bad surprises.
Consistent quality in manufacturing
Consistent quality also starts with the product design (we do DFM reviews on custom parts and custom assemblies to ensure they can be made with a low quality risk – see examples of common issues on metal cast parts or on plastic injected parts).
In our assembly operations, we also try hard to simplify and mistake-proof the work. When we prepare productions in relatively large volumes, we usually perform risk analyses and a control plan.
Problem-solving and improvement
Our quality engineers study the failures we detect as part of our inspections & testing. We also encourage our customers to gather information about their customers’ complaints & returns. There is often a lot to learn, to improve the product or process design and reduce risks in the future.
We maintain batch-level traceability. This is a must in order to support a root cause analysis and a rapid investigation, to isolate the products concerned in case of a containment, and to minimize the financial impact of a serious issue.
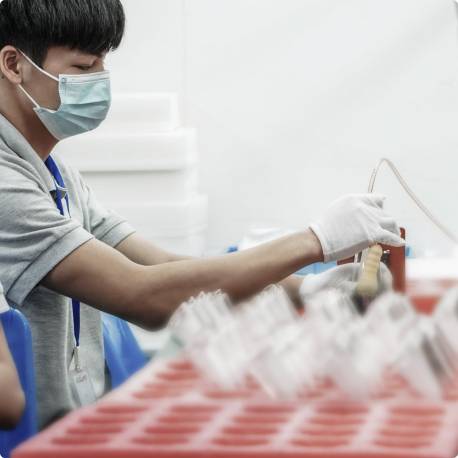
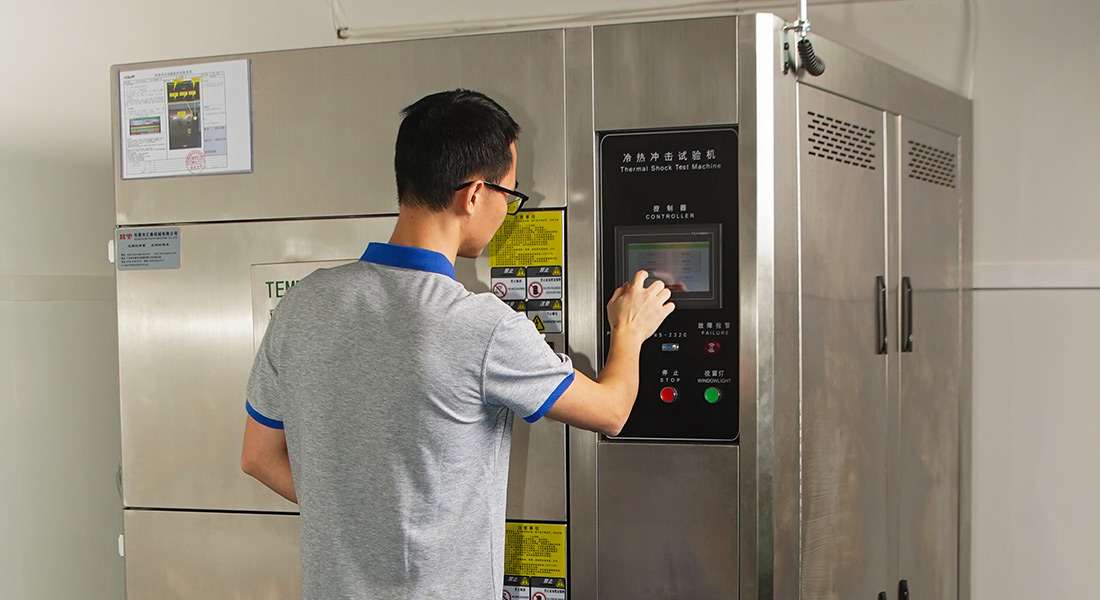
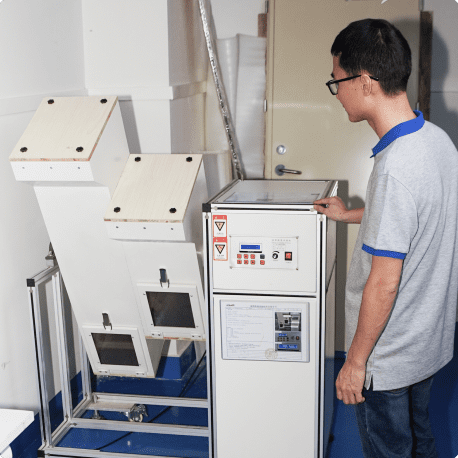
Product compliance testing
We work with local and international testing laboratories that are ISO 17025 certified for that type of work. Our customers receive the full reports and/or certificates, including the detailed testing report with data collected and conclusions.
Environmental management system
Our environmental management system (certified to the ISO 14001 standard by BSI) ensures we remain in compliance with relevant regulations and the products we make don’t contain substances that are detrimental to human health in dangerous levels.
A whole product safety plan
- A list of applicable regulations and requirements
- Product design reviews, verification plans, and reliability test reports (and, if applicable, redesign iterations and their test reports)
- A list of component suppliers and proofs that they were qualified in a structured manner
- Process FMEA and process control plan
- Failure analyses, countermeasures, and follow up on the effectiveness of countermeasures
- Product compliance testing reports and/or certificates
With all that in hand, your chances of being accused of negligence are minimized as much as is possible.