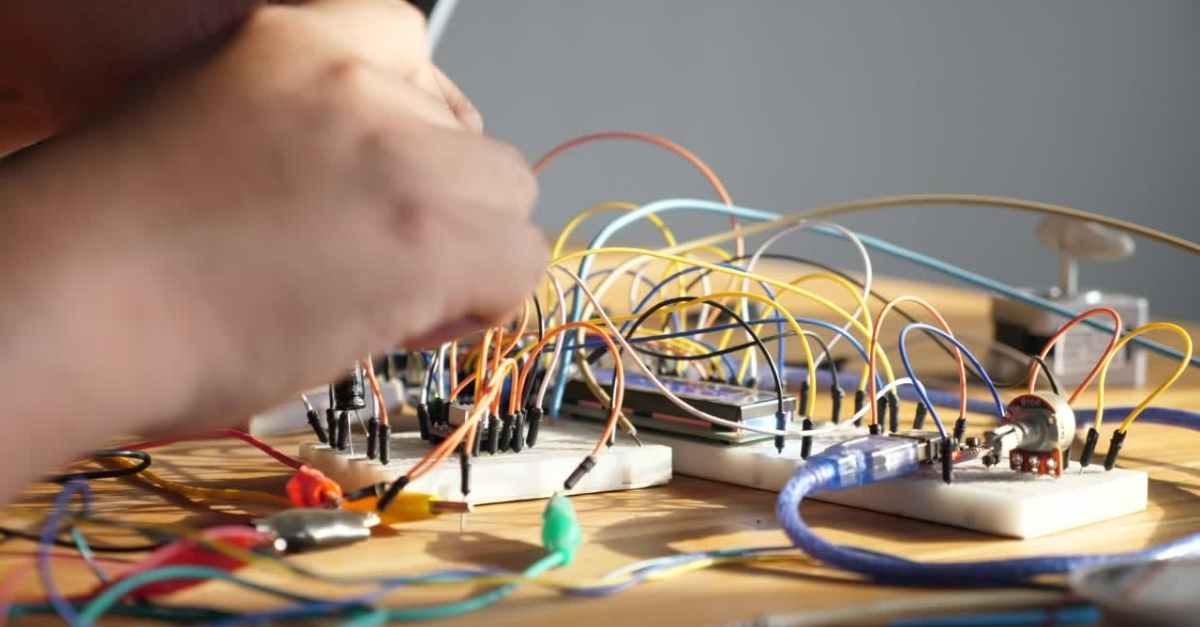
If you’re going to manufacture a mechanical and/or electrical product in China, this article will help you plan for the steps to follow to get prototypes made before going into mass production.
Why a prototype is required?
You might need a concept of the product, to show investors and to launch a Kickstarter campaign.
You probably need a prototype that is close to the final version of the product, in order to run testing (including usability testing) and validate the design before going into production.
When making prototypes in China, the usual process goes as follows (The 5 steps are often overlapping, but for clarity let’s break them down one by one):
Step 1: Design the product
We are talking CAD drawings, PCBA schematics, and so on. Do this yourself (or through a design firm working for you), so that you own all the blueprints from the start. Don’t make the mistake of having a Chinese manufacturer do it, as they will almost certainly consider that they own all intellectual property rights.
We discussed this assumption about owning IP rights for products they help develop in this episode of Sofeast’s podcast: Sourcing Chinese Manufacturers: Western Or Chinese Model?
Step 2: Check and confirm that all parts of the product can be made/purchased
The parts need to be purchased and/or fabricated before a prototype can be assembled.
This is when someone has to start working on sourcing. Depending on the complexity of the prototype, it might take some time. It will confirm whether cost targets are achievable and will uncover some of the technical difficulties (what parts, if any, are hard to find in China).
Many shortcuts can be taken at this stage. Typically, the plastic and metal parts that have to be custom-made can be fabricated without investing in expensive tooling (that comes later in the process, once there is less uncertainty).
In case the product includes a very specialized module that is central to overall performance/design, it is better to do the hard work of identifying and qualifying the supplier and to have that supplier start working on customizations (if any), at this stage. This is often a complex sub-assembly that becomes a project in itself.
Step 3: Assemble the prototype
Once all the parts are ready, the assembly can take place. Feedback such as “these 2 components are hard to kit together” is very important and will call for changes.
After that, many other issues are typically found. For example:
- Functionality issues
- Performance issues (e.g. much tuning is needed)
- Poor ergonomy for users
- Overall ‘look’ issues (a glossy part does not match with a matte part, etc.)
At this stage, design and prototyping iterations are often necessary until all major issues have been addressed.
Step 4: Tooling for production
Once a prototype has been made with final parts and has been approved, tooling can be ordered. For example, a plastic injection mold for the casing. (Make sure you have the right type of contract before wiring any money — read this article on the China Law Blog.)
Do a first article validation on a few parts made with the new tooling, and sign off if all is acceptable.
Do not forget testing equipment, which sometimes takes weeks or months to prepare.
Step 5: Tests and validations
You want to avoid unpleasant surprises in production. Spend some time at this stage to do in-depth testing (you can see how thorough the testing and validation process is in this blog post: How Many Product Samples Are Required For Reliability & Compliance Testing?):
- For compliance (safety, battery cells…)
- For performance, including stress testing
- For robustness
- For the use of key features
Many people are tempted to go into production as early as possible. However, an issue discovered before production starts is much faster and much cheaper to fix (by a factor of 10, 50, or 100).
For similar reasons, it is usually considered a must to do at least 1 pilot run before launching mass production.
For more context on bringing a new product to life, I suggest you watch this video on this topic:
Need help with your prototyping and new product development?
Here at Agilian we can build fully functional prototypes and have an in-house laboratory to test them. Our experienced engineers:
- Perform DFM reviews on your design to suggest changes at an early stage
- DO R&D work to develop a prototype that can be more easily manufactured
- Develop your tooling
- Create rapid prototypes using our in-house equipment such as 3D printers and CNC machines
- Source your components from trustworthy suppliers
- Assure the product complies with your market’s regulations
- Do validation runs (pilot runs) & testing of the entire product
- Follow a proven NPI process giving clear structure and reducing production risks
You’re welcome to speak with us if you have any questions about getting your product developed and prototypes made and tested.